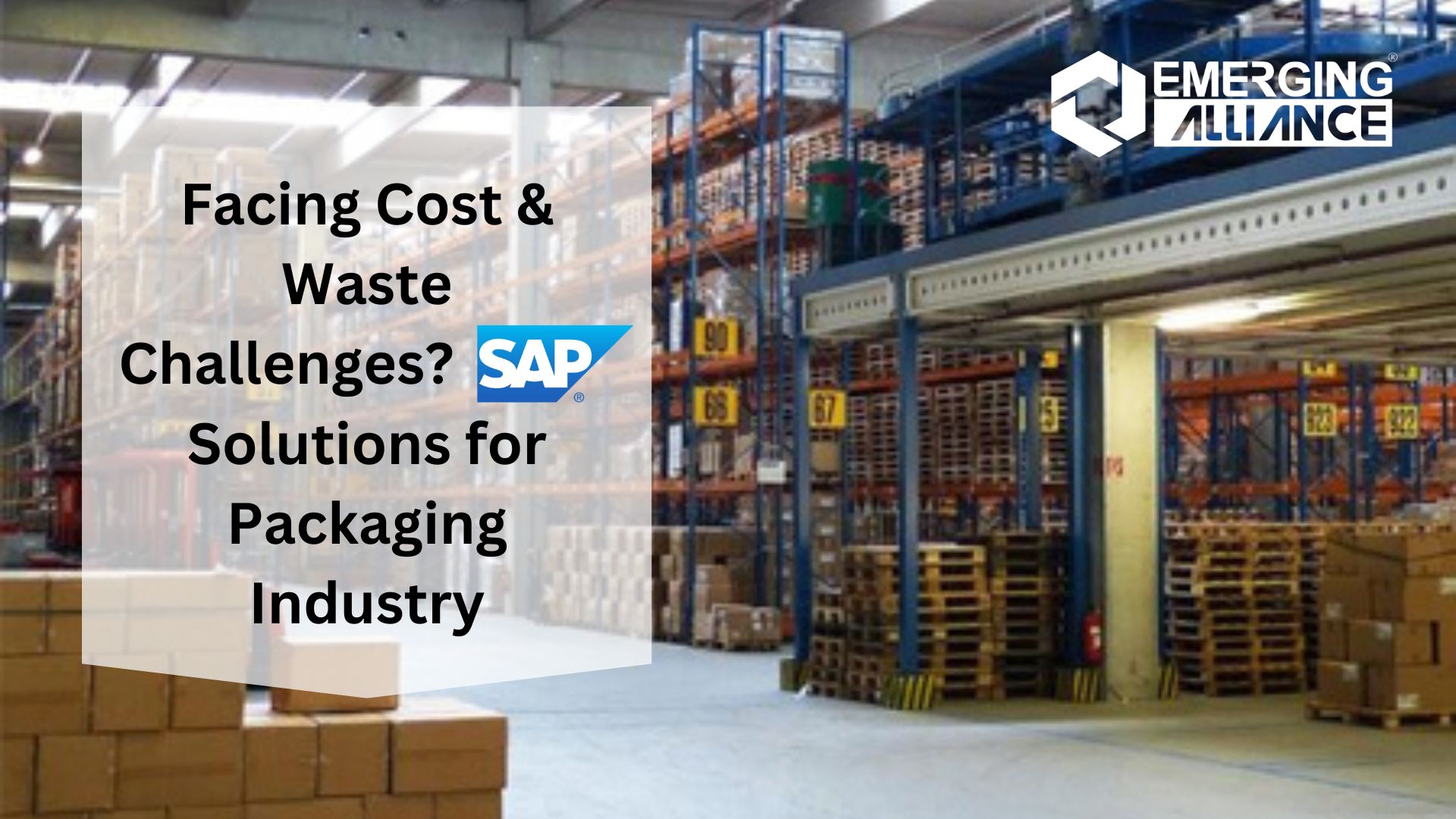
Facing Cost & Waste Challenges? SAP Solutions for Packaging Industry
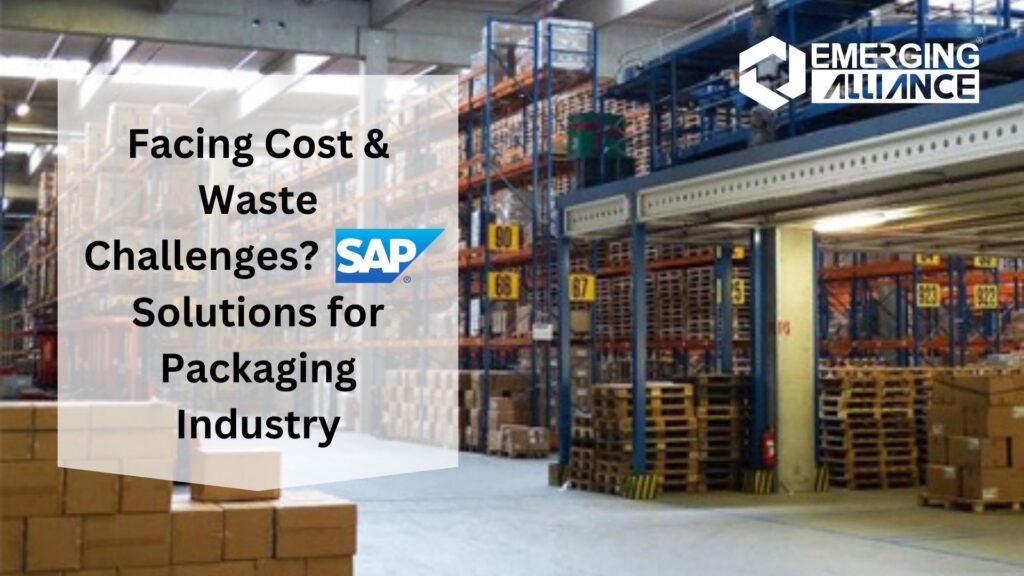
Optimize Packaging Operations: SAP Solutions for Cost Control & Waste Reduction
Managing costs and reducing waste are paramount to sustaining profitability and improving operational efficiency. The packaging industry faces constant pressure to meet market demands, improve production timelines, and maintain sustainability—all while controlling expenses. One of the most effective ways to tackle these challenges is by implementing SAP solutions that streamline processes, reduce operational inefficiencies, and enhance resource management.
Understanding the Cost & Waste Challenges in the Packaging Industry
The packaging industry is confronted with several cost-related and waste-management issues, including:
- Rising Raw Material Costs: Fluctuating raw material prices can significantly affect packaging companies’ profit margins. Packaging companies often find it difficult to accurately forecast material requirements, leading to over-ordering or stock shortages.
- Inefficient Production Processes: Without the right tools and technology, production processes may suffer from inefficiencies, leading to increased downtime, longer production cycles, and higher labor costs.
- Waste Management: Packaging companies generate substantial amounts of waste, both in terms of excess raw materials and finished goods that do not meet quality standards. Managing and reducing waste requires an integrated approach to inventory control, quality assurance, and resource allocation.
- Sustainability Pressures: Consumers and governments are increasingly demanding eco-friendly packaging solutions. Meeting these requirements while maintaining profitability presents a delicate balance for packaging manufacturers.
How SAP Solutions Address These Challenges
SAP solutions are designed to tackle the core pain points of the packaging industry, helping businesses drive down costs, reduce waste, and increase overall efficiency. Here’s how SAP can help:
1. Streamlined Inventory Management
One of the primary drivers of inefficiency in the packaging industry is poor inventory management. Over-ordering raw materials or mismanaging stock levels can lead to excess costs and waste.
With SAP Inventory Management capabilities, companies can get real-time visibility into inventory levels and improve the accuracy of their forecasts. By utilizing data-driven insights, SAP helps companies manage their supply chains more effectively, ensuring that materials are ordered only when needed and are used efficiently during production.
2. Optimized Production Planning
Inefficiencies in production planning are a major source of waste and increased costs. SAP Production Planning (SAP PP) allows businesses to plan and monitor the entire production process, ensuring that raw materials are used effectively and production runs at optimal efficiency. SAP also helps in tracking machine downtime, minimizing bottlenecks, and optimizing labor usage to maximize output.
3. Enhanced Quality Management
Quality issues not only result in wasted materials but also impact customer satisfaction. With SAP Quality Management (SAP QM), packaging companies can integrate quality checks into every stage of the production process. This proactive approach minimizes defects, reduces rework, and helps meet industry standards, reducing the costs associated with poor-quality products.
4. Data-Driven Waste Reduction
SAP’s Advanced Analytics and Reporting tools enable packaging businesses to identify areas where waste can be reduced. By analyzing production data, companies can pinpoint inefficiencies in their processes—whether it’s material waste, machine downtime, or quality-related issues—and implement targeted improvements.
5. Sustainability Compliance and Reporting
As sustainability becomes an ever-more important factor in packaging, SAP solutions help companies align with environmental goals and regulations. SAP’s Environment, Health, and Safety (EH&S) module helps companies manage their environmental footprint by tracking energy usage, material recycling, and waste management practices. This is critical for businesses looking to enhance their eco-friendly initiatives without compromising profitability.
6. Cost Transparency and Financial Management
Controlling costs is essential in the packaging industry. SAP Financial Management solutions provide in-depth cost tracking, helping businesses monitor expenses at every level of the production process. With clear visibility into financials, companies can identify areas for improvement and implement cost-saving measures effectively.
The Benefits of SAP Implementation for the Packaging Industry
Implementing SAP solutions in the packaging industry provides several key advantages:
1. Improved Operational Efficiency
With integrated systems that connect inventory, production, quality, and financial management, SAP streamlines processes, reduces redundancy, and minimizes errors. This leads to faster production cycles, lower overhead, and reduced downtime.
2. Cost Reduction
By improving inventory management, production planning, and quality assurance, SAP helps reduce both direct and indirect costs. With accurate forecasting and waste reduction strategies, packaging companies can better control expenses and improve their bottom line.
3. Waste Minimization
Through real-time data insights and advanced analytics, SAP enables packaging companies to reduce waste across the production cycle. Whether it’s raw materials, excess inventory, or inefficient production processes, SAP helps minimize waste and promotes sustainability.
4. Compliance and Sustainability
With increasing pressure to meet environmental standards, SAP ensures that packaging businesses comply with global sustainability requirements. By optimizing resource use and improving reporting, companies can demonstrate their commitment to environmental stewardship.
5. Scalability and Flexibility
As the packaging industry evolves, companies need solutions that can adapt to changing market conditions. SAP’s scalable solutions allow businesses to scale their operations efficiently, whether they are dealing with increased demand or adapting to new industry trends.
Why Choose SAP Implementation for Your Packaging Industry?
The complexity of the packaging industry demands robust, flexible, and integrated solutions to address the ongoing challenges of cost and waste management. SAP offers an unparalleled suite of tools that support businesses in streamlining their operations, improving efficiency, and cutting down on unnecessary costs.
If you are looking to future-proof your packaging business and reduce operational waste, SAP implementation is a strategic investment that can deliver long-term benefits. By adopting SAP solutions, you can stay ahead of the competition, drive sustainability, and enhance profitability.
Cost and waste management challenges are a constant hurdle for packaging businesses, but with SAP solutions, there is a way forward. By implementing SAP’s comprehensive suite of tools, packaging companies can tackle inefficiencies head-on, reduce costs, minimize waste, and embrace sustainability.
If you’re ready to transform your packaging operations, SAP implementation could be the key to unlocking new levels of operational excellence. Reach out to SAP consultants today to learn how these solutions can streamline your business and give you a competitive edge in the packaging industry.
Ready to dive deeper into the topics you love? Visit our website to explore a treasure trove of valuable content, resources, and insights that will captivate your mind and fuel your curiosity!
Want to speak to an expert? Fill in the form below, and we will be in touch with you shortly!