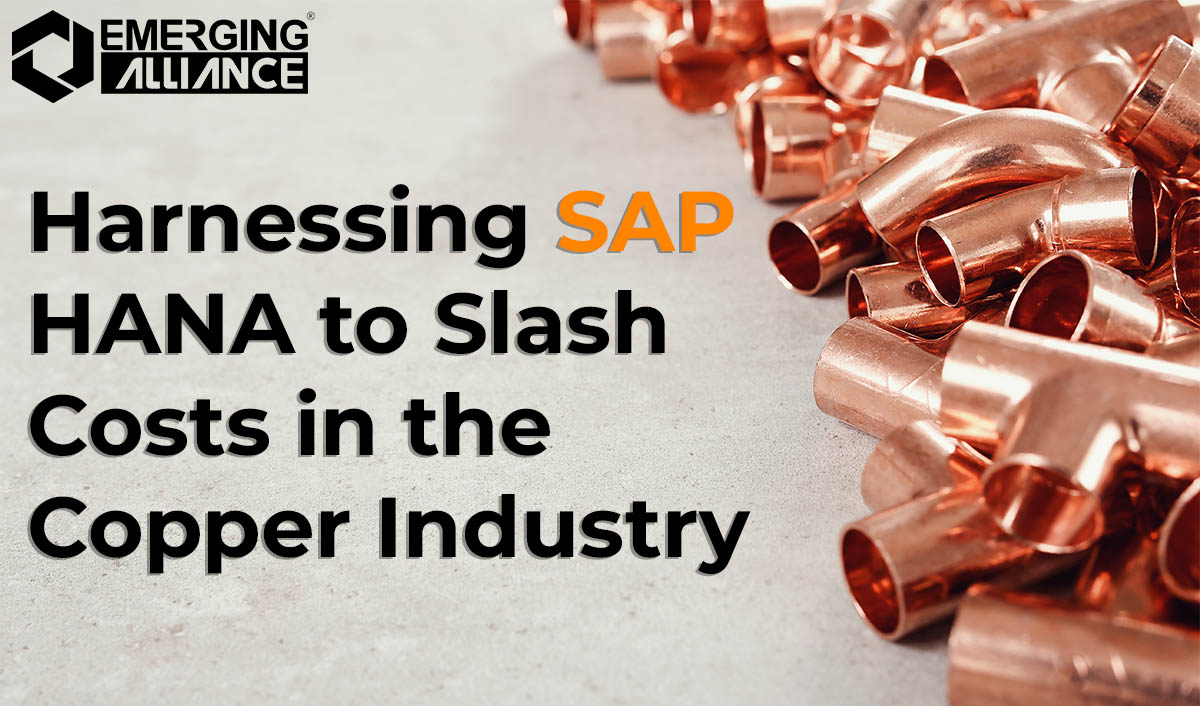
Harnessing SAP HANA to Slash Costs in the Copper Industry
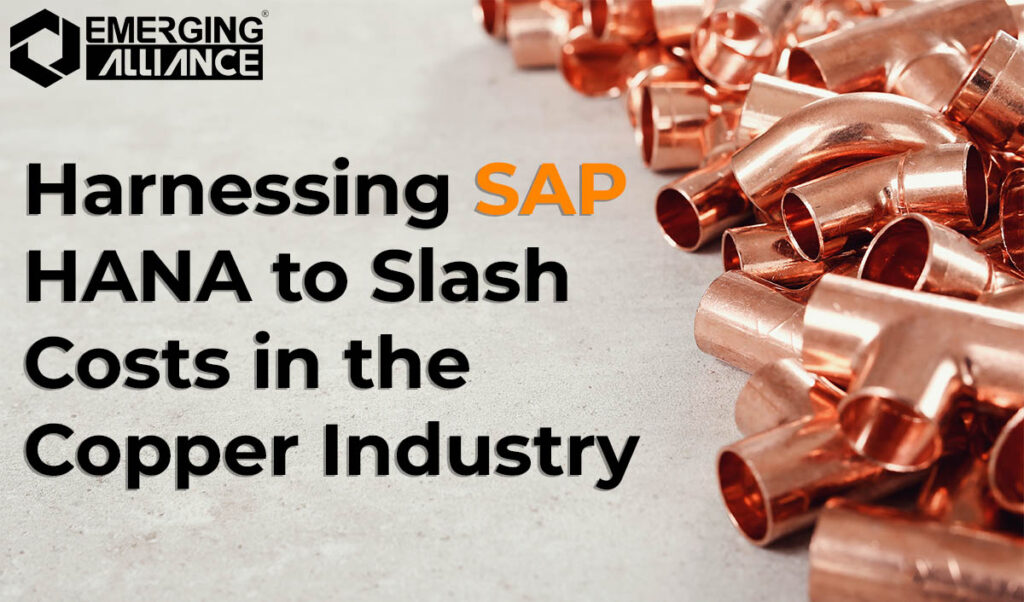
Know How SAP HANA Revolutionizes the Copper Industry
SAP HANA, a high-performance in-memory database management system, offers several features that can help address cost issues in the copper industry. Here are some key features of SAP HANA that can be leveraged:
SAP HANA and Real-time analytics:
SAP HANA enables real-time data processing and analytics, allowing copper companies to make informed decisions quickly. By accessing real-time data on production, costs, and market conditions, organizations can optimize their operations and identify cost-saving opportunities promptly.
Predictive analytics:
SAP HANA includes advanced predictive analytics capabilities, which can help copper companies forecast demand, optimize production processes, and identify cost-saving measures. By analyzing historical data and patterns, organizations can make proactive decisions to optimize costs and reduce waste.
Supply chain optimization with SAP HANA for Copper Industry:
SAP HANA’s powerful data processing capabilities enable effective supply chain management. Copper companies can use the platform to integrate and analyze data from various sources, such as suppliers, production facilities, and logistics providers. By optimizing the supply chain, organizations can reduce transportation costs, improve inventory management, and minimize disruptions.
Energy management with SAP HANA:
The copper industry is energy-intensive, and managing energy costs is crucial for profitability. SAP HANA’s energy management features can help monitor and optimize energy consumption in real time. By collecting data from sensors and meters, organizations can identify energy inefficiencies, optimize equipment performance, and reduce energy costs.
Cost transparency and reporting with SAP HANA for Copper Industry:
SAP HANA provides powerful reporting and analytics capabilities, enabling copper companies to gain insights into cost structures and identify areas of improvement. The platform allows for detailed cost analysis, cost allocation, and variance reporting. By understanding cost drivers and monitoring costs in real time, organizations can implement cost-saving measures effectively.
Integrated planning and budgeting for Copper Industry:
SAP HANA enables integrated financial planning, budgeting, and forecasting. Copper companies can use the platform to create accurate and detailed budgets, track actual costs against budgeted values, and perform scenario analysis to optimize cost management. By aligning financial plans with operational goals, organizations can proactively manage costs and improve profitability.
Machine learning and AI capabilities in SAP HANA:
SAP HANA supports machine learning and artificial intelligence algorithms, which can be leveraged to automate and optimize various processes in the copper industry. For example, predictive maintenance algorithms can help reduce equipment downtime and maintenance costs, while AI-driven demand forecasting models can optimize inventory levels and reduce carrying costs.
By leveraging these features of SAP HANA, the copper industry can improve cost management, increase operational efficiency, and enhance overall profitability. It is worth noting that the specific implementation and customization of SAP HANA would depend on the unique requirements and challenges faced by each copper company.
To know more about our products and services, visit us at: https://emerging-alliance.net/