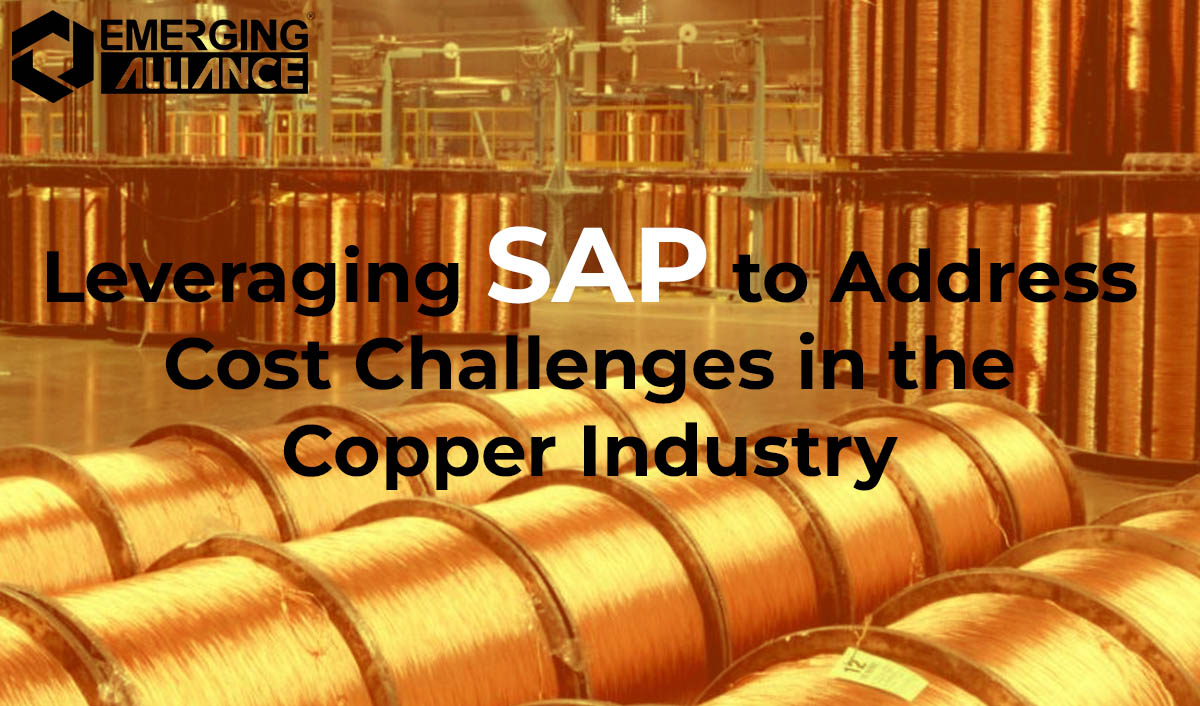
Leveraging SAP to Address Cost Challenges in the Copper Industry
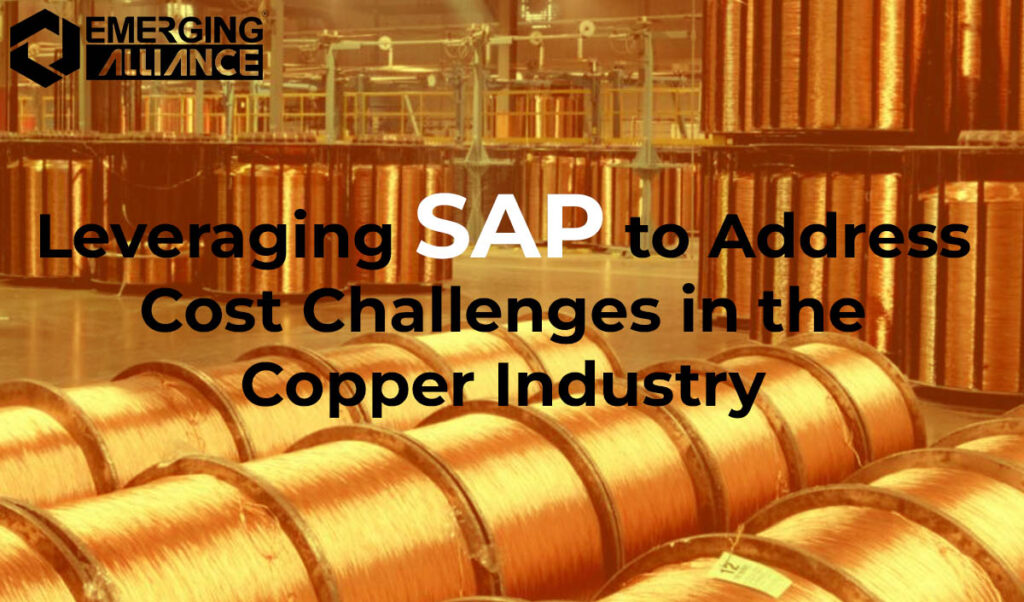
How to drive Cost Efficiency in the Copper Industry with SAP?
In the highly competitive copper industry, managing costs effectively is crucial for ensuring profitability and maintaining a competitive edge. To tackle cost-related challenges, the copper industry can turn to SAP (Systems, Applications, and Products) — a leading provider of enterprise resource planning (ERP) software solutions. Thus, copper industry can improve overall financial performance by leveraging SAP.
Supply Chain Management:
SAP’s supply chain management (SCM) module empowers copper mining companies to optimize material flows, streamline procurement processes, and enhance inventory management. By efficiently managing the supply chain, mining companies can reduce costs associated with inventory holding, transportation, and procurement, ultimately enhancing operational efficiency.
Production Planning in SAP for Copper Industry:
The production planning module within SAP enables copper mining companies to create accurate production schedules, manage capacity effectively, and optimize resource utilization. By leveraging these capabilities, companies can reduce production costs and minimize costly downtime, leading to improved productivity and operational efficiency.
Asset Management:
Effective management of mining assets is vital for cost control and maximizing equipment performance. SAP’s enterprise asset management (EAM) module allows copper mining companies to proactively maintain and manage their assets, including mining equipment and infrastructure. By implementing preventive and predictive maintenance strategies, mining companies can optimize equipment performance, minimize unplanned downtime, and reduce maintenance costs, ultimately improving cost efficiency.
Financial Management in SAP for Copper Industry:
SAP’s financial management module provides comprehensive tools for managing financial processes. These include budgeting, cost accounting, and financial reporting. By leveraging these features, copper mining companies can gain a clear understanding of cost drivers, analyze profitability, and make informed decisions to optimize cost structures. Accurate cost accounting and financial reporting enable companies to identify areas for cost reduction, ultimately enhancing financial performance.
Project Management in SAP for Copper Industry:
In the copper industry, effective project management is critical for controlling costs and ensuring timely completion. SAP’s project management module helps mining companies plan, execute, and monitor projects efficiently. By utilizing this module, copper mining companies can control project costs, mitigate risks, and optimize resource allocation, ultimately leading to improved project outcomes and cost efficiency.
Business Intelligence and Analytics:
SAP’s business intelligence (BI) and analytics capabilities provide powerful tools for data analysis, reporting, and decision-making. By leveraging these features, mining companies can gain valuable insights into their operations, identify cost-saving opportunities, and make data-driven decisions to optimize processes and reduce costs. The ability to access real-time data and perform comprehensive analysis empowers mining companies to proactively identify cost inefficiencies and take corrective actions promptly.
Energy Management in SAP for Copper Industry:
Energy consumption is a significant cost factor in the copper industry. SAP offers energy management solutions that help mining companies monitor and optimize energy consumption. By analyzing energy data, identifying inefficiencies, and implementing energy-saving measures, copper mining companies can reduce energy costs, enhance sustainability efforts, and improve their bottom line.
Supplier Relationship Management:
SAP’s supplier relationship management (SRM) module helps streamline supplier management processes, negotiate better terms, and optimize procurement activities. By effectively managing supplier relationships, copper mining companies can reduce procurement costs, enhance supply chain efficiency, and gain a competitive advantage. SAP’s SRM module facilitates improved collaboration and transparency with suppliers, leading to cost savings and improved procurement processes.
Cost Controlling in SAP for Copper Industry:
SAP’s cost controlling module enables copper mining companies to monitor and control costs across various areas of their operations. By implementing cost control measures, analyzing cost variances, and conducting cost-benefit analyses, mining companies can identify cost-saving opportunities, optimize cost structures, and drive operational efficiency. SAP’s cost controlling capabilities provide companies with the tools to proactively manage costs and make informed decisions to improve financial performance.
Why SAP for Copper Industry?
In the dynamic and cost-sensitive copper industry, leveraging SAP’s extensive suite of modules can provide mining companies with the necessary tools to address cost-related challenges effectively. By utilizing SAP’s features, including supply chain management, production planning, asset management, financial management, project management, business intelligence, energy management, supplier relationship management, and cost controlling, copper industry players can optimize their operations, enhance cost control, and drive financial performance.
To know more about our products and services, visit us at: https://emerging-alliance.net/