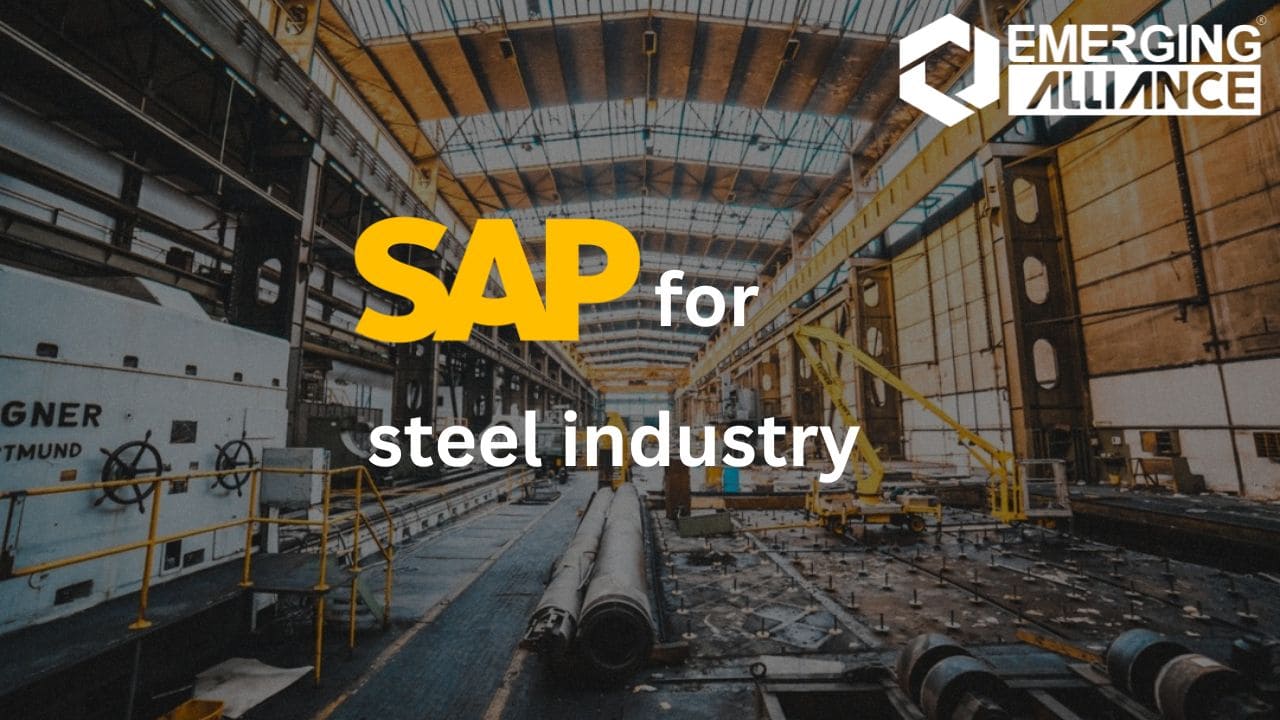
SAP for the Steel Industry
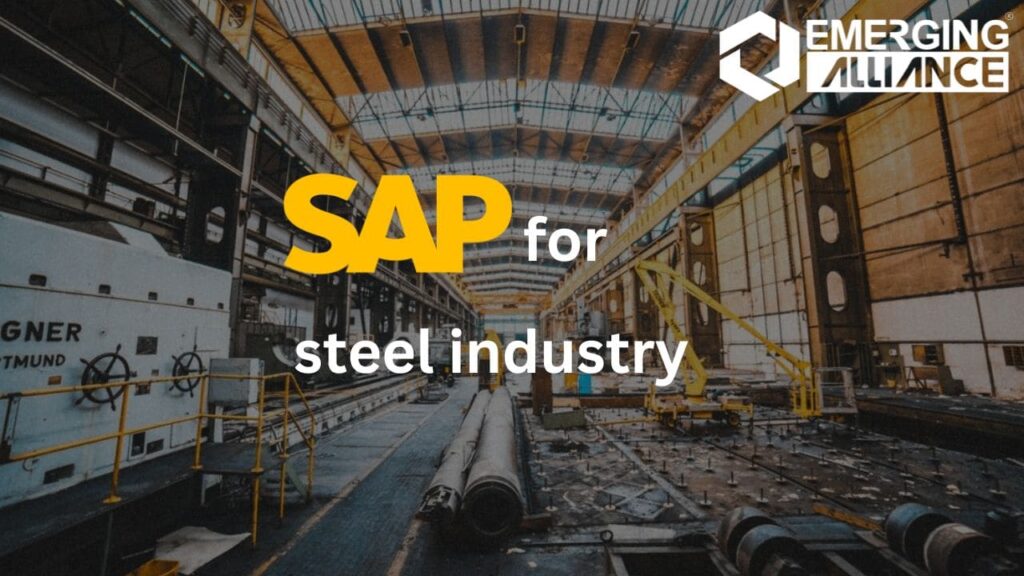
Enhancing Supply Chain Management: SAP Solutions for Steel Companies
SAP for the Steel Industry streamlines and optimizes critical processes, from order to cash and procure to pay, to sales orders and production management. SAP enables steel industries to achieve greater operational efficiency and overall performance. With features like accurate product costing, invoicing, and service management, this ERP solution proves indispensable for steel companies striving to maintain a competitive edge in today’s dynamic market landscape.
The primary modules of the SAP ERP System for Steel Industries are as follows:
Order to Cash:
- SAP for the Steel Industry enables receiving a customer inquiry, and the Engineering team creates a Bill of Material for the product, estimating the cost and plan.
- The sales team then prepares a commercial quote and submits it to the customer.
- Upon receiving a purchase order from the customer, a sales order is created in SAP.
- This triggers the production of the finished goods (FG), followed by the generation of an accounts receivable invoice and an incoming payment.
- Important reports include Customer receivables, Cash flow, and Sales analysis.
Procure to Pay:
- Utilizing the MRP function SAP system for the Steel Industry auto-creates purchase requests based on the Bill of Material (BOM).
- These purchase requests are converted into purchase orders for the procurement of materials.
- Goods receipt is recorded upon the delivery of goods.
- Payable invoices and outgoing payments are processed.
- Essential reports cover Vendor payables, Cash flow, Purchase analysis, Minimum order quantity, re-order quantity, and lead days.
Sales Order:
- Sales orders of SAP for the Steel Industry are created once purchase orders are raised or customer quotations are confirmed.
- Relevant documents and information are attached using DMS (Document Management System).
- Payment terms and delivery dates are finalized, and order acknowledgments are sent via email.
Sales Quote:
- Sales quotations are provided to customers and can be converted into orders.
- The quotation is closed once it is confirmed.
MRP (Material Requirements Planning):
- MRP is utilized for production planning, considering raw material availability and open purchase orders.
- This is a critical aspect of the Plan to Produce process.
Purchase Request:
- Purchase requests can be auto-created by the Material Requirements Planning system or generated manually based on departmental requirements.
- Purchase orders are subsequently generated based on these requests.
Purchase Order:
- Purchase orders are created following an approval procedure.
Goods Receipt Purchase Order (GRPO):
- Goods receipts are posted against purchase orders when vendors deliver items.
- This action updates inventory levels in the warehouse.
Supplier Payment:
- Supplier invoices are recorded based on GRPO.
- Outgoing payments are processed in response to these invoices.
Production:
- Production orders are auto-created based on the Bill of Material (BOM), demand, and stock levels as per MRP.
- Raw materials are issued following defined route stages.
- Upon completing all stages, production receipts are recorded, and finished goods are added to inventory.
- Accurate product costing is a critical aspect of SAP.
Invoicing:
- Accounts payable and receivable invoices are created, followed by posting payment entries.
- The Open Document system ensures proper financial control.
Service:
- Equipment cards are auto-created for each serial number and dispatched item.
- Service calls are generated based on equipment cards, and associated costs are recorded at regular intervals.
These are some of how SAP significantly benefits the Steel Industry, enhancing operational efficiency and overall performance.
To learn more about our services, visit us at: https://emerging-alliance.net/