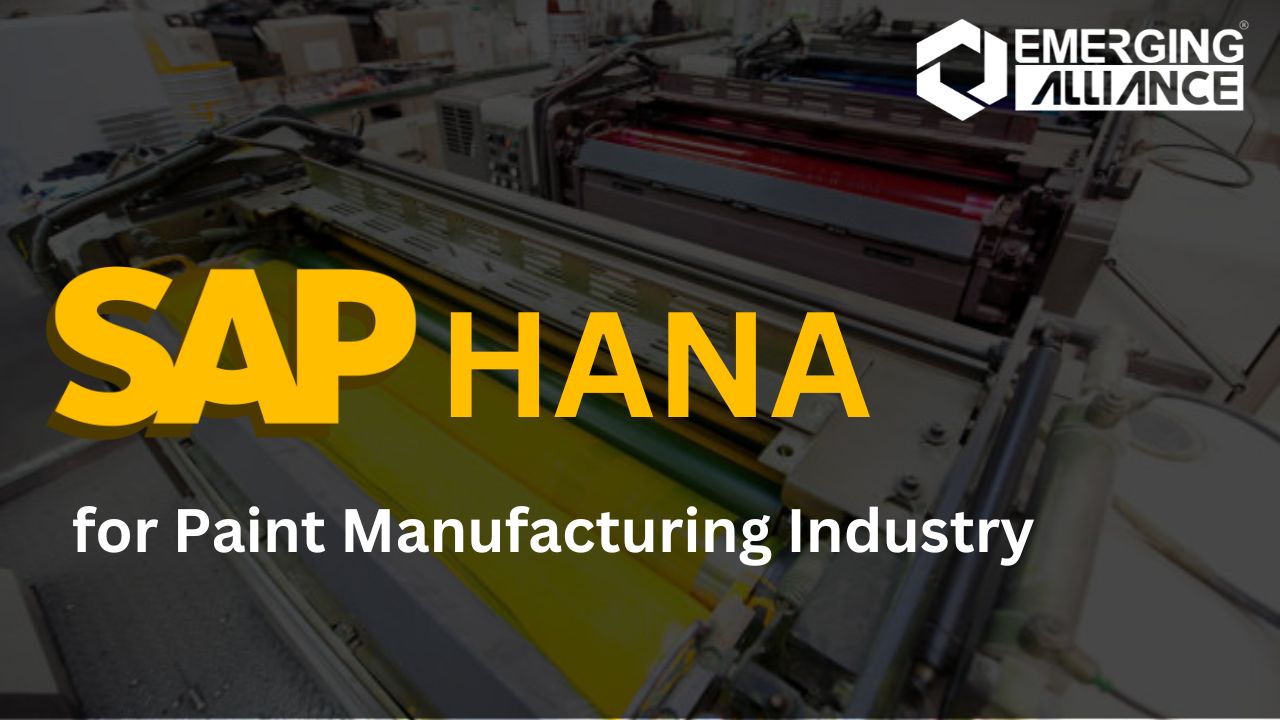
SAP HANA for Paint Manufacturing Industry | SAP S/4HANA
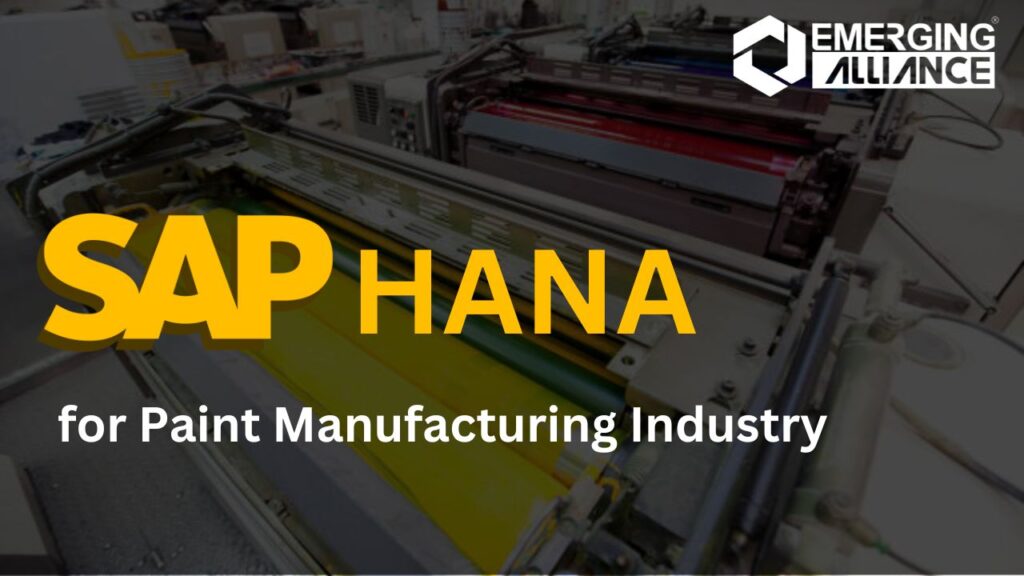
Future-Proofing Your Paint Business: Harnessing SAP HANA for Long-Term Success
The paint manufacturing industry, recognized for its adaptability, continuously evolves to meet evolving demands. To maintain a competitive edge in this dynamic landscape and optimize business processes, innovative software solutions are essential. In such a context, SAP HANA emerges as the leading ERP solution for sectors like paint manufacturing, enabling efficient management of operations from anywhere in the world. Transitioning to SAP HANA software is the ideal choice to address the challenges inherent in the paint manufacturing industry.
Let’s explore how SAP S/4HANA strengthens the paint manufacturing sector:
Order to cash:
In the make-to-stock and order process of paint manufacturing, the workflow proceeds as follows:
Upon receipt of yearly/quarterly or time-based blanket agreements/contracts from customers, SAP HANA facilitates the creation of purchase orders as blanket agreements or sales orders. This initiates continuous production of finished goods (FG) in periodic orders. Subsequently, the process involves accounts receivable invoices and incoming payments, with key reports including customer receivables, cash flow, and sales analysis.
Procure to pay:
Using the MRP function, procurement planning for the month begins at the start of each month. Purchase requests are automatically generated, followed by goods receipts against these requests by the stores. Subsequently, accounts payable invoices and outgoing payments are processed according to accounting requirements, with major reports covering vendor payables, cash flow, and purchase analysis.
Sales order:
Sales orders originate from blanket agreements, upon raising POs, or upon confirmation of quotations by customers in the paint manufacturing industry. SAP HANA allows seamless attachment of soft copies of POs via the document management system (DMS), while also enabling setting payment terms and delivery dates. Order acknowledgments are then sent via email directly from SAP HANA.
Sales quote:
Upon confirmation of sales quotations, SAP HANA seamlessly converts them into orders, effectively concluding the quotation process.
MRP:
Material Requirements Planning (MRP) plays a crucial role in production planning and raw material procurement, considering existing stock levels and demand. This aspect also includes the plan-to-produce process.
Purchase request:
PRs are automatically generated by Material Requirements Planning, complemented by manual creation of PRs department-wise for office equipment, consumables, etc. SAP HANA then generates purchase orders against these requests.
Purchase order:
POs are created based on purchase requests, facilitated by approval procedures. For items with default suppliers, SAP HANA automatically generates POs through MRP, fetching unit costs from predefined price lists.
GRPO:
Upon delivery of items by vendors based on POs, goods receipts against purchase orders are posted, resulting in inventory debits and stock additions in the warehouse (WMS).
Supplier payment:
Supplier invoices are generated based on GRPO, against which outgoing payments are executed.
Production:
Aligned with the Bill of Materials (BOM), production orders are automatically generated by SAP HANA, considering demand and stock levels determined by MRP. Raw materials are issued route stage-wise, with completion of all stages resulting in production receipts, thereby adding finished goods to inventory. Product costing is a critical aspect of SAP HANA in this process.
Invoice:
Account payable invoices are generated, followed by the posting of payment entries, with the open document system ensuring proper control.
This outlines how SAP HANA ERP software transforms operations within the paint manufacturing industry, significantly enhancing overall efficiency and productivity.
To learn more about our SAP services and solutions, visit us at: https://emerging-alliance.net/